“今年以來,車間職工主動承接400個K車車門加工自營工程,為處節約成本60萬元......”12月25日,鐵運處車輛段修車車間主任束慶武在四季度標準化班組成果展示會上說道。
鐵運處車輛段修車車間主要負責南部地區808輛自備車輛維修、臨修及其他工程車輛維修任務,僅年度材料費支出就是一筆不小的數字。車輛段引導修車車間職工牢固樹立過“緊日子”的思想,通過自主加工、“五小”創新、搭建平臺等方式,促進創新創效落到實處。
自主加工,打造增效新引擎——
“平時注重自制加工、修舊利廢,用自制品替代外購品”
“修車車間任務重、人員少,今年減員12人,在完成82輛大修、500多輛段輔修、200多輛臨修等本職工作的前提下,利用休班的時間承攬自營工程,是件不容易的事,職工真正憑借技術降成本。”車輛段副段長王洪強說。
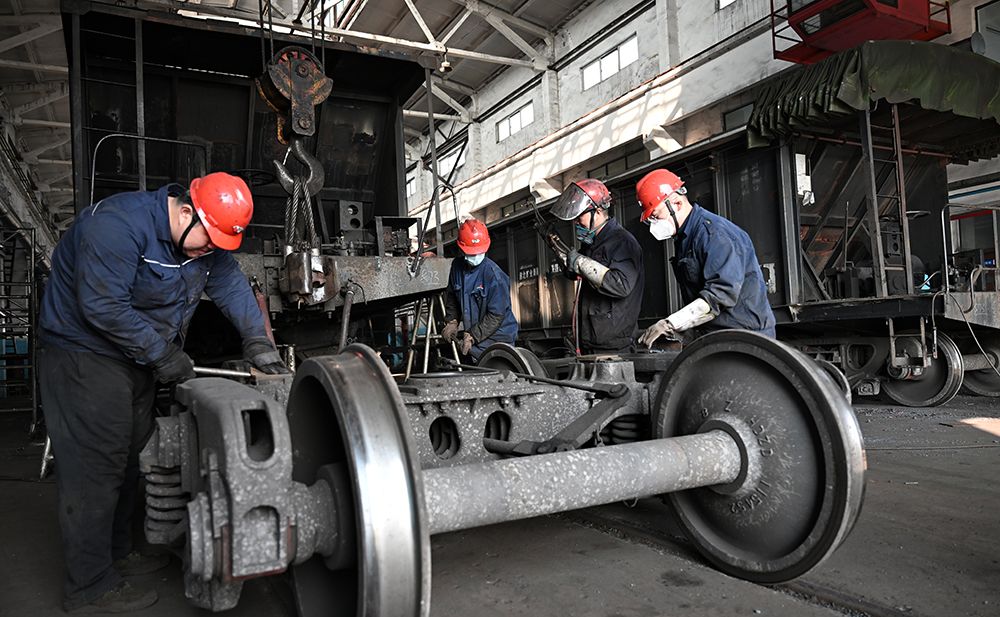
自主加工車門職工第一次干,行業地方鐵路也沒有經驗可學,從檢修工藝、尺寸、工具等,完全是摸著石頭過河。職工現場畫圖、集思廣益、群策群力,確保加工的車門能夠滿足不同車門類型需求。
“不止加工車門,這個車間平時注重自制加工、修舊利廢,用自制品替代外購品。這是他們自制加工的渦輪箱底座,這個是120閥架子……”王洪強帶著筆者一路走、一路介紹,車間的自主維修,讓人眼界大開。一年來,該車間自制儲風缸底座及梁200個,制動缸底座110個,彎管160根,自制各類角鐵230根等等,節約成本25萬余元。
注重創新,提升工作效能——
“每一次的小創新都是一個遇到難題、解決難題、積累經驗、開拓思路的過程”
在修車車間,車間主任束慶武打開話匣子,說起了他們為加裝K車底開門自制加工成套作業模具的“路線圖”。
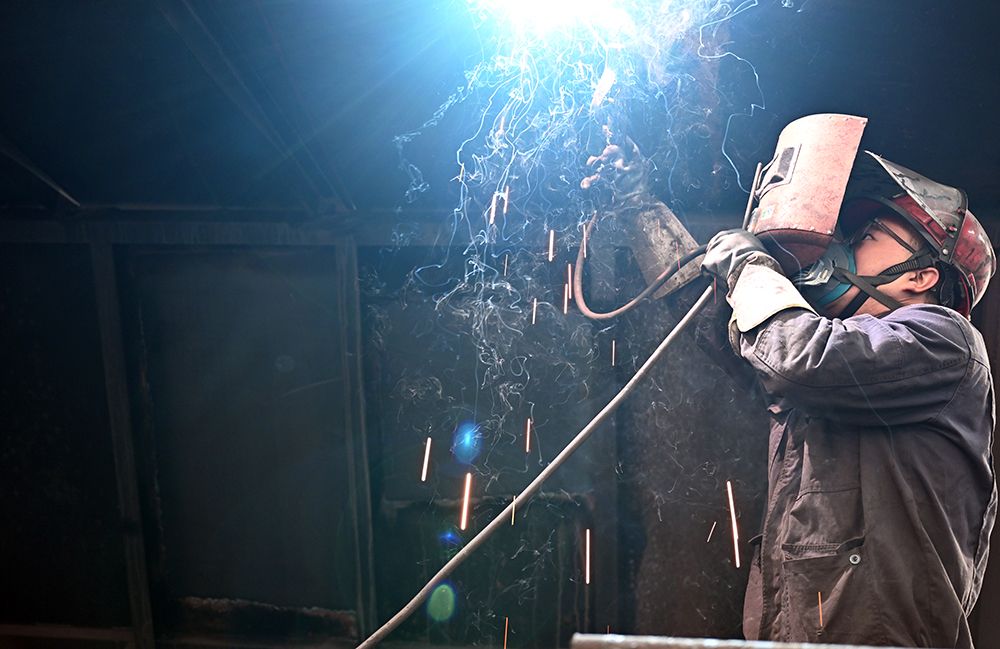
開始,他們一天只能加裝1個車門,效率比較慢。職工在一起碰撞思想,設計一款含組裝、焊接、調節、噴漆、運輸一體化作業模具,實現車門加工框架固定、對接、全面焊接、噴漆、運輸功能,極大提高了工作效率。
“每一次的小創新都是一個遇到難題、解決難題、積累經驗、開拓思路的過程”束慶武說。在車間,職工的小發明都是在工作實踐中摸索出來的。針對K車在長期運行中,由于裝卸及操作不規范等問題會造成車門間隙越來越大,漏灑煤炭,污染道床現象,他們通過優化車門底邊技術改造,實現車門下部及側面“零間隙”密貼。今年,這項K車車門間隙控制裝置榮獲國家發明專利。
自制的雙向作用風缸地面檢修試驗裝置,不僅解決了受車上作業空間受限影響帶來的操作不便等問題,還減少了職工勞動作業強度。僅此一項,可節約資金40萬元,受到同行業的認可。車輛車鉤鉤頭專用吊具、鐵路貨車腳蹬調整裝置、K型煤炭漏斗車應急關門裝置等多項技改,接地氣、實用性強。該車間還對污水處理裝置進行改進,通過加裝限位器、污水泵等,降低刷車水耗,提高水重復利用率。
搭建平臺,激發創效活力——
“現在,有活職工愿意主動干”
“該車間為職工搭建了交流學習、考核激勵、互助成長三個平臺,現在,有活職工愿意主動干。”該段黨支部書記李紅旗說。
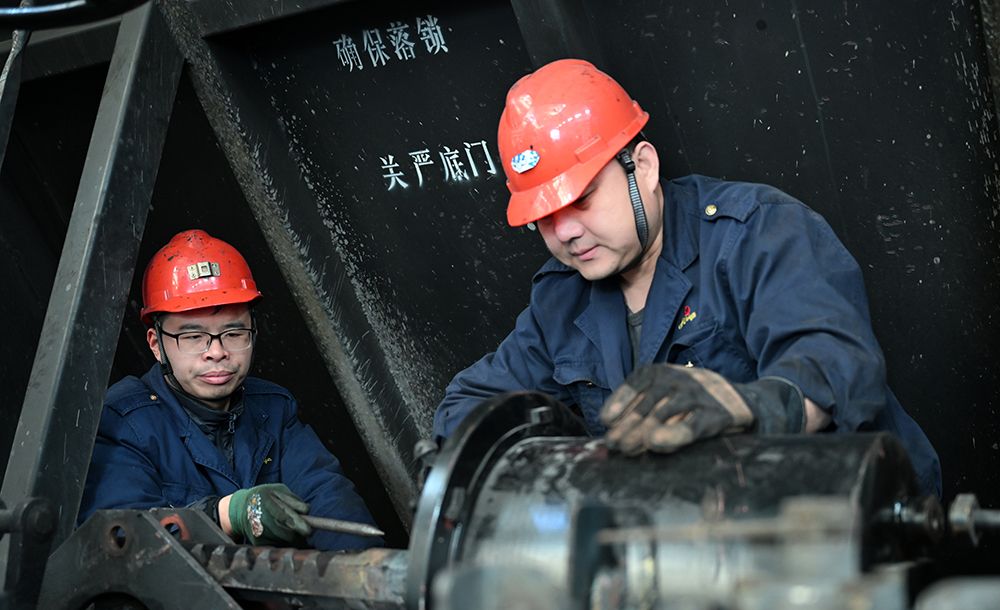
搭建職工交流學習平臺,鼓勵技術能手,開展“大拿上講臺”,對作業人員進行實操輪訓,并兌現培訓市場化工資。結合車間生產需求因需施教,不定期開展技能提升培訓和小型設備使用復訓,多措并舉提升職工接受新設備、掌握新技術的積極性和主動性,職工技能水平進一步提升,修車效率和修車質量不斷提高。
搭建考核激勵平臺,車輛段在班組與班組內部實行“鏈式結算”,建立科學、規范的內部市場化考核機制,讓職工知道干好干壞不一樣,激勵職工努力工作、提高效率,形成“比學趕幫超”的良好氛圍。
搭建互助成長平臺,充分發揮“K車工作室”作用,讓有經驗的技術骨干和業務骨干帶領新職工一起工作、學習和成長。通過簽訂“師帶徒”協議,明確培養內容,建立培訓效果考核兌現機制,激發職工的學習熱情和創效智慧。兩年來,職工鄭海在集團技術比武中獲得“技術狀元”,張國防和朱旭在集團“名師高徒”大賽中分別獲得首席名師、首席高徒稱號。
(審核:尹良功 責編:尹杰)